THE HEART
OF A ROCKET
Since the beginning of Japan's space development program (more than four decades ago), Mitsubishi Heavy Industries (MHI) has played a leading role in the manufacturing of the country's launch vehicles.
From design and manufacturing, to assembly and the launch itself, the manufacturing and engineering giant's expertise and experience has since served Japan well, giving the country a competitive edge in the global market.
But even with all that experience, placing a launch vehicle into space - a brutal and unforgiving environment - is no easy task. Billions of dollars of precision engineering, scientific equipment and more must all hold up in an alien atmosphere. Plus, of course, it has to get to space in the first place. So, what does it take? Simple: a powerful, world-class engine. But building one? That's a bit more complicated…
ENGINE SIMPLICITY:
A COMPLEX ART
Currently, MHI and JAXA are hard at work on the H3 - Japan's first new launch vehicle in 30 years, which also features a brand new engine, the LE-9. "Developing a new engine can take 10 years or more," explains Makoto Arita, Sub-Manager of the H3 Launch Vehicle Project Team at JAXA.
“IF YOU INCLUDE THE TIME SPENT ON THE LE-9 ENGINE, AND ON THE LE-X, WHICH WAS THE MODEL PREVIOUSLY DEVELOPED DURING THIS RESEARCH, OUR TOTAL COMES TO ALMOST 10 YEARS.”
Across that decade of tireless development, the two organizations believe they have succeeded in creating an engine that is world-class and has the potential to be world-leading. Not through making things more complicated, but by simplifying. One such key innovation on the LE-9 is the use of a simpler engine cycle - officially called an "expander bleed cycle" - which eliminates the need for the complex burner system more commonly found on most other rockets. This not only improves reliability (because there's less to go wrong), but also reduces production cost.
LE-9'S EXPANDER BLEED CYCLE
WORLD'S FIRST STAGE ENGINE WITH NO AUXILIARY COMBUSTION CHAMBER
Another upgrade has been a move away from using high-pressure gas to operate valves. By using electronic drive valves, the risk of gas leaks is eliminated and the engine is more reliable as a result. Simple. Only it wasn't - this particular innovation delivered an unforeseen challenge for the MHI engineers.
Electronic drive valves require a large amount of power in order to work, which means they require a high-voltage motor. However, a high-voltage motor emits electromagnetic noise. During testing and development, that becomes a problem for sensors that monitor heat, pressure, and even acceleration, which need to process exceptionally weak signals with high precision. After painstakingly identifying the source and paths of the noise, altering wiring and adding in electrical grounding, the team successfully reduced the noise to acceptable levels.
This year, MHI moves into testing the first and second stages of the launch vehicle. A "hold-down" test of the second stage is expected to be conducted towards the end of 2019 or early 2020 at MHI's Rocket Engine Combustion Test Facility in northern Japan. The entire rocket, including the first stage, will then begin its hold-down tests at the Tanegashima Space Center in southern Japan in 2020.
These tests involve the engine being held down - literally - by giant clamps, as engineers push it through various thrust values while closely monitoring for even the tiniest abnormalities. If anything adverse is detected, the engine is safely shut down, before solutions are engineered across the ensuing months.
3D PRINTING
SPACE PARTS
One of the reasons the LE-9 engine and H3 rocket will be so cost-effective, is 3D printing. For components such as complex piping - previously hewn from giant chunks of metal or made by bending and welding together metal sheets - industrial 3D printing technology now allows for seamless production in a shorter period of time.
Through all of this innovation and more, the LE-9 engine certainly does have the potential to be world-leading. But as we speak, Japan is already eyeing another new development on the horizon, beyond even the ambition of the LE-9 powered H3: reusable rockets. JAXA has already, in fact, developed a reusable liquid oxygen-liquid hydrogen engine, and are busy planning a test of it in a seven-meter tall rocket with a mass of two tons. A test flight to 100 meters is also in the pipeline. The goal? Understand the reusable process and figure out how best to lower operational costs.
There's even a launch date in mind: 2025. Ambitious for anyone else, perhaps, but from this partnership? It's already proven itself across space vehicle design, manufacturing, assembly and launch. It's proven its reliability. And it's never once rested in its mission to deliver next-generation space vehicles that give Japan access to a market once dominated by a select few governments and companies. Start the countdown…
READ MORE
THE BIRTH OF A ROCKET
What does it take to launch the H3 rocket and what does it mean for Japan and the world?
Find out more >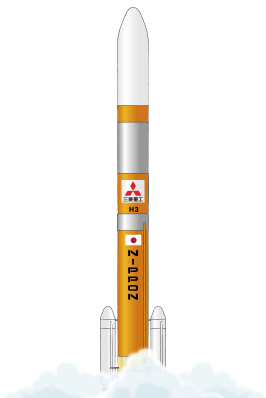